The structural part of HAWC2 is based on a multibody formulation using the floating frame of reference approach. In the particular formulation of the code, the turbine structure is subdivided into a number of bodies, where each body has its own coordinate system. Within each body, the structure consists of an assembly of linear Timoshenko beam elements. The nonlinear effects of the body motion (rotations and deformations) are accounted for in the coupling constraints in between the individual bodies. Small deflections are assumed within the linear beam elements. This means that effects of large rotations and deflections are included using a proper subdivision of a blade to a number of bodies. The bodies representing the mechanical parts of the turbine are connected by joints, also referred to as constraints.
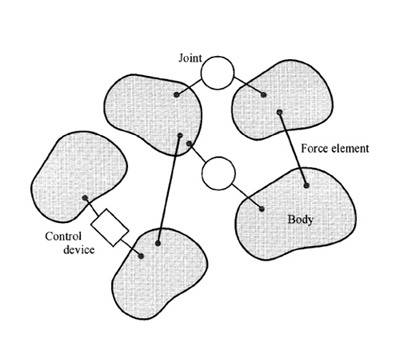
The constraints are formulated as algebraic equations, which impose limitations of the bodies’ motion. This formulation is quite general, and could in principle just be a trajectory which the body needs to follow. So far the constraints implemented for turbine simulation are: fixed connection to a global point (e.g. tower bottom clamping), fixed coupling of relative motions (e.g. fixed pitch or yaw), frictionless bearings, and bearings with rotation angles controlled by the user. The code will account for inertial forces, also when rotations of bodies are externally specified. External forces are in general placed on the structure in the deformed state, which is especially important for pitch loads and twist of the blades. Since large rotations are handled by a proper subdivision of bodies, the code is also particularly well suited for calculations on very flexible turbines subjected to, for instance, large blade deflections.
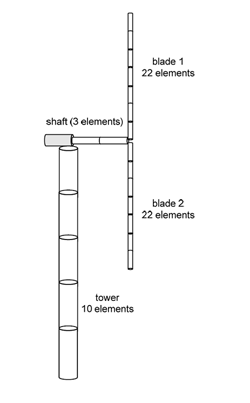
The structure is represented by a specified number of bodies and beam elements in space. The multibody formulation gives a great flexibility and HAWC2 is able to simulate many different structures. This is especially relevant for offshore turbines where the support structure can be quite complex like jackets etc. Masses and inertia can be added as remote masses and inertia which is linked to the main body. Structural property input for advanced components like the blade can be can be calculated by the cross section analysis tool BECAS. Another option for the structural input is to use an anisotropic fully populated stiffness matrix beam element (BECAS output data). The multibody formulation used in HAWC2 is based on the theory described in [1] and [2].
[1] A.A.Shabana. "Dynamics of Multibody Systems". Cambridge University Press, University of Illinois at Chicago, 2nd edition, 1998.
[2] Kim, T, Hansen, AM, and Branner, K. “Development of an anisotropic beam finite element for composite wind turbine blades in multibody system”. Renewable Energy, 59, 172-183, 2013.